Upcoming Events
Stay tuned for more upcoming events!
Greenleaf Introduces Greenleaf-360: A New Carbide End Mill Product Line
Published August 15, 2022
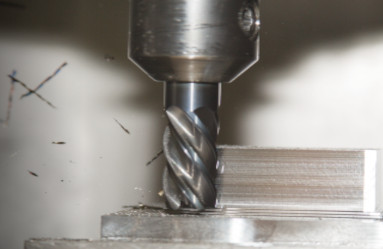
Today Greenleaf announced the release of a new carbide end mill product line: Greenleaf-360. This sub-micron grade with 10% cobalt provides toughness and wearability to offer customers one grade to be applied in many applications
Multipurpose Mills
Published June 14, 2022
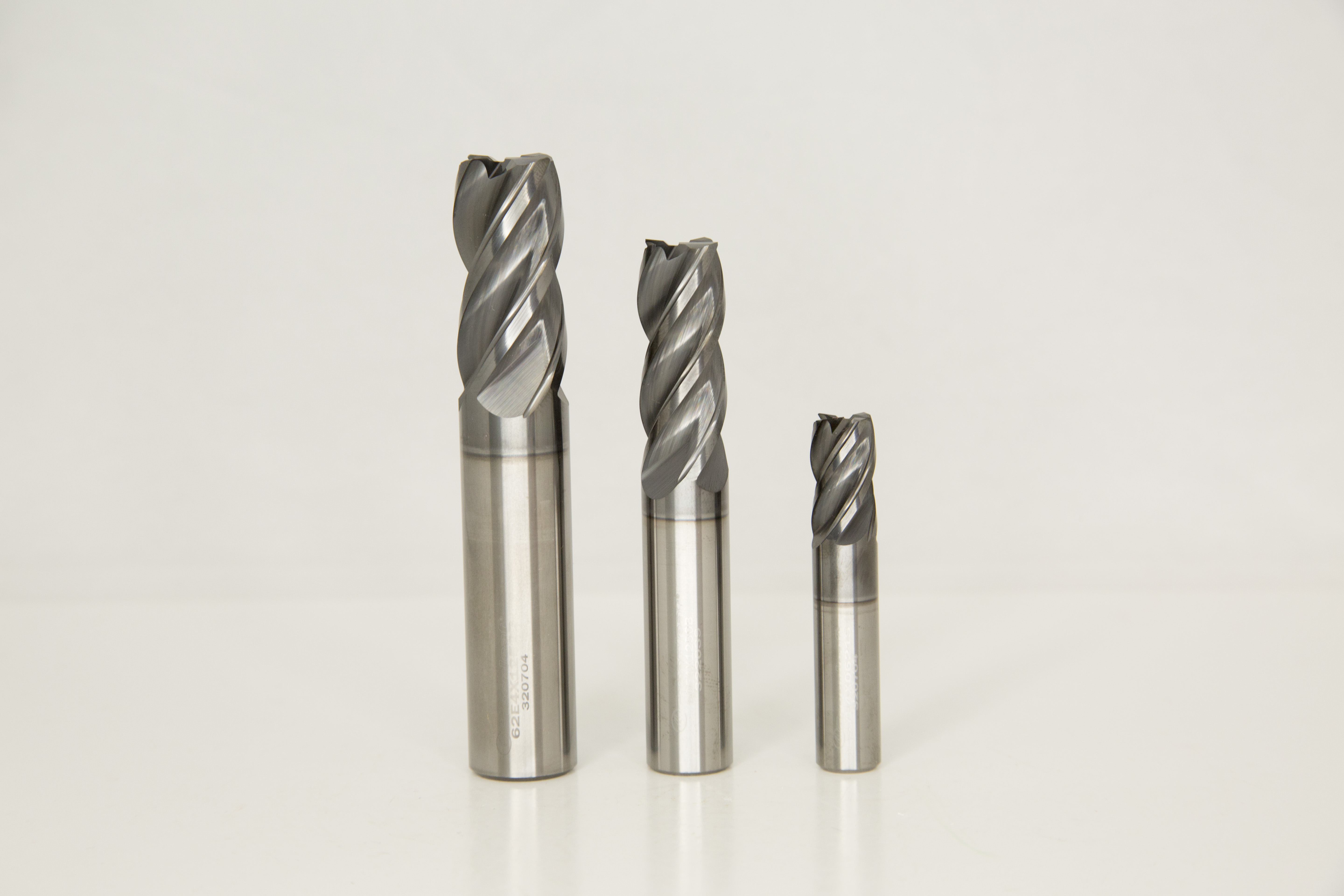
For machining operations in which change is a constant, general-purpose endmills can have a value that far exceeds their actual cost. As the name suggests, these endmills are not designed for a specific cutting application or material. Instead, they are tools that can be used for most standard machining jobs.
Ask the Expert: Martin
Published May 23, 2022
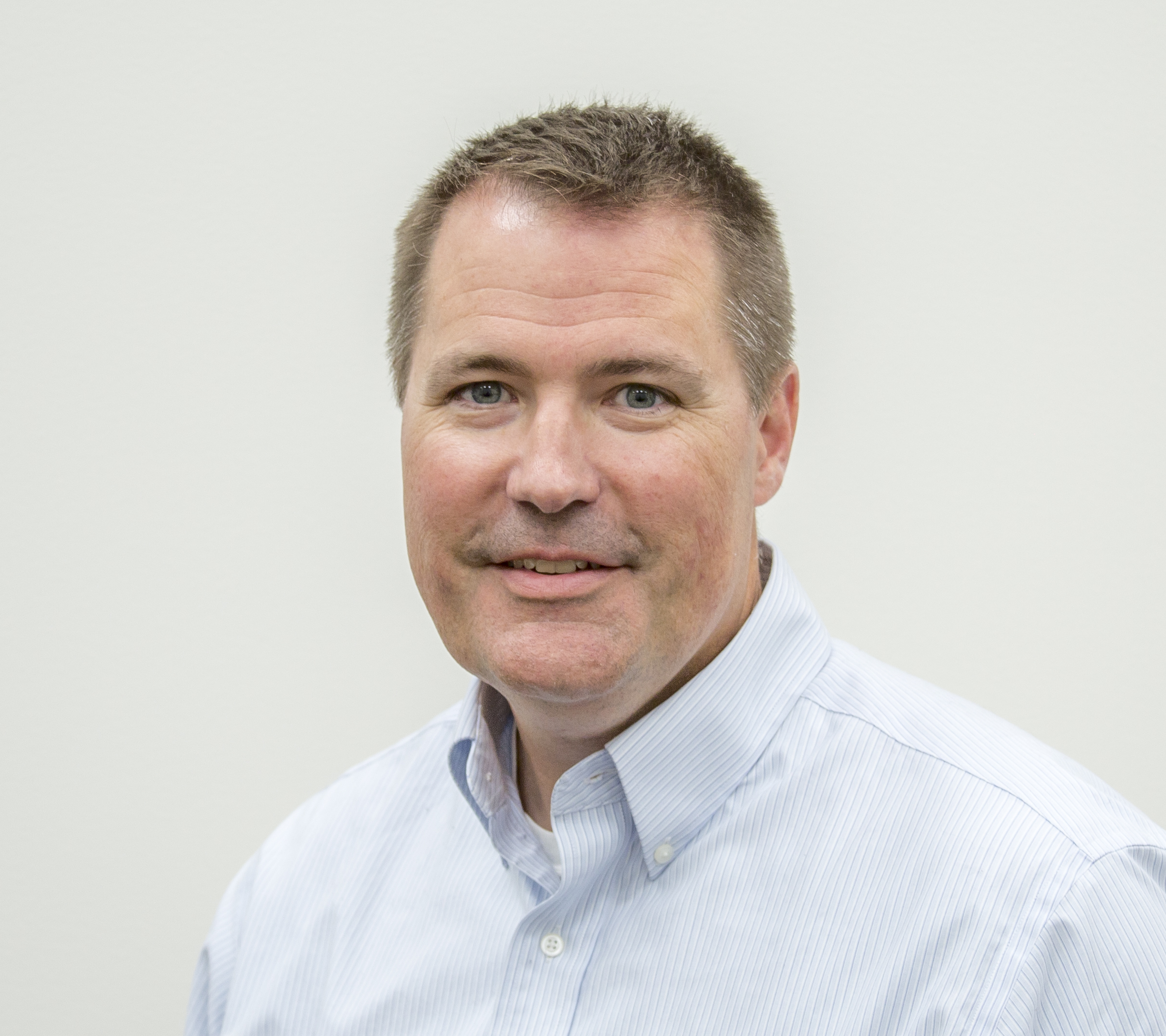
All of Greenleaf’s sales engineers receive extensive product and technical training, and many have previous experience in manufacturing. This guarantees our customers an experienced engineer to help develop solutions for higher productivity.
Don’t Let Interruptions Slow You Down
Published February 21, 2022
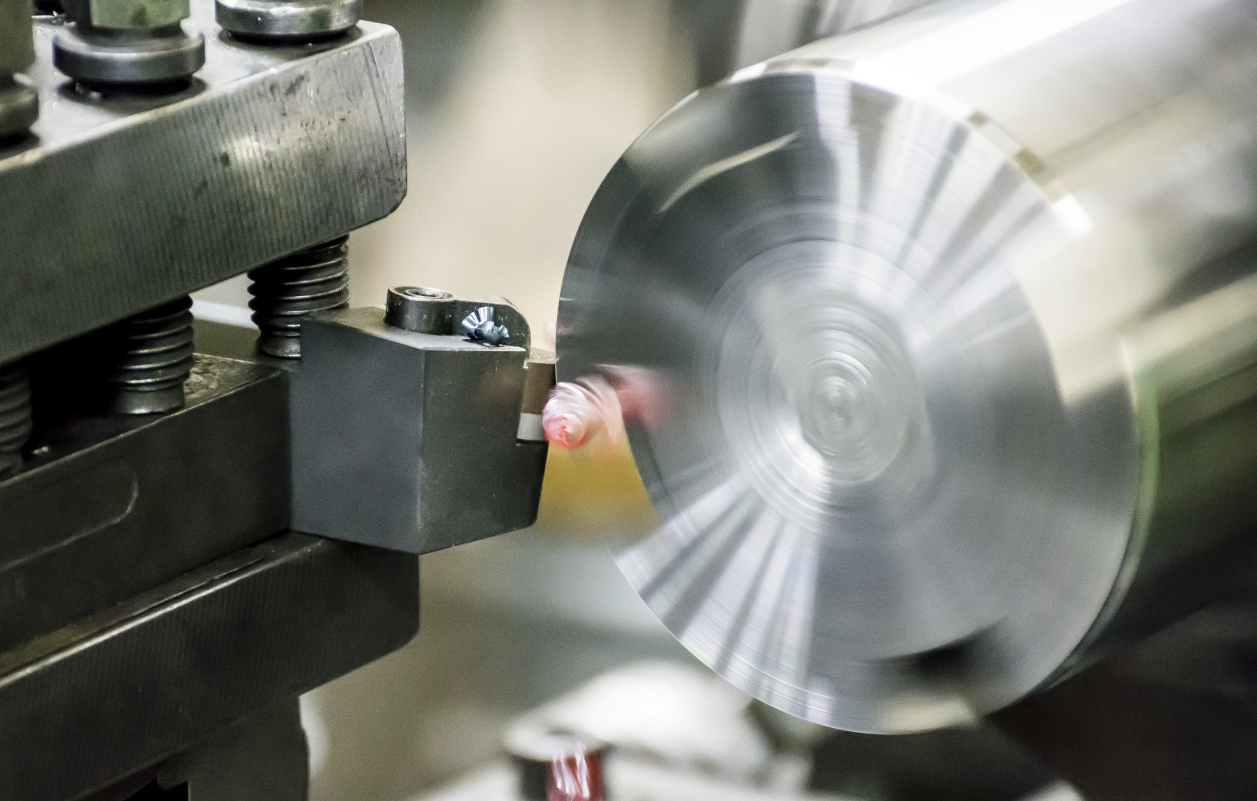
Interrupted cutting in turning is subjective. While some operators may look at a part with a keyway and a small depth of cut as a heavy interruption, another operator may classify heavy interruptions only as multiple interruptions with a larger depth of cut. The workpiece material, part configuration and features, and depth of cut will all come into play when determining how the interruption will affect the overall process.
Cutting Tools For All Occasions
Published February 14, 2022
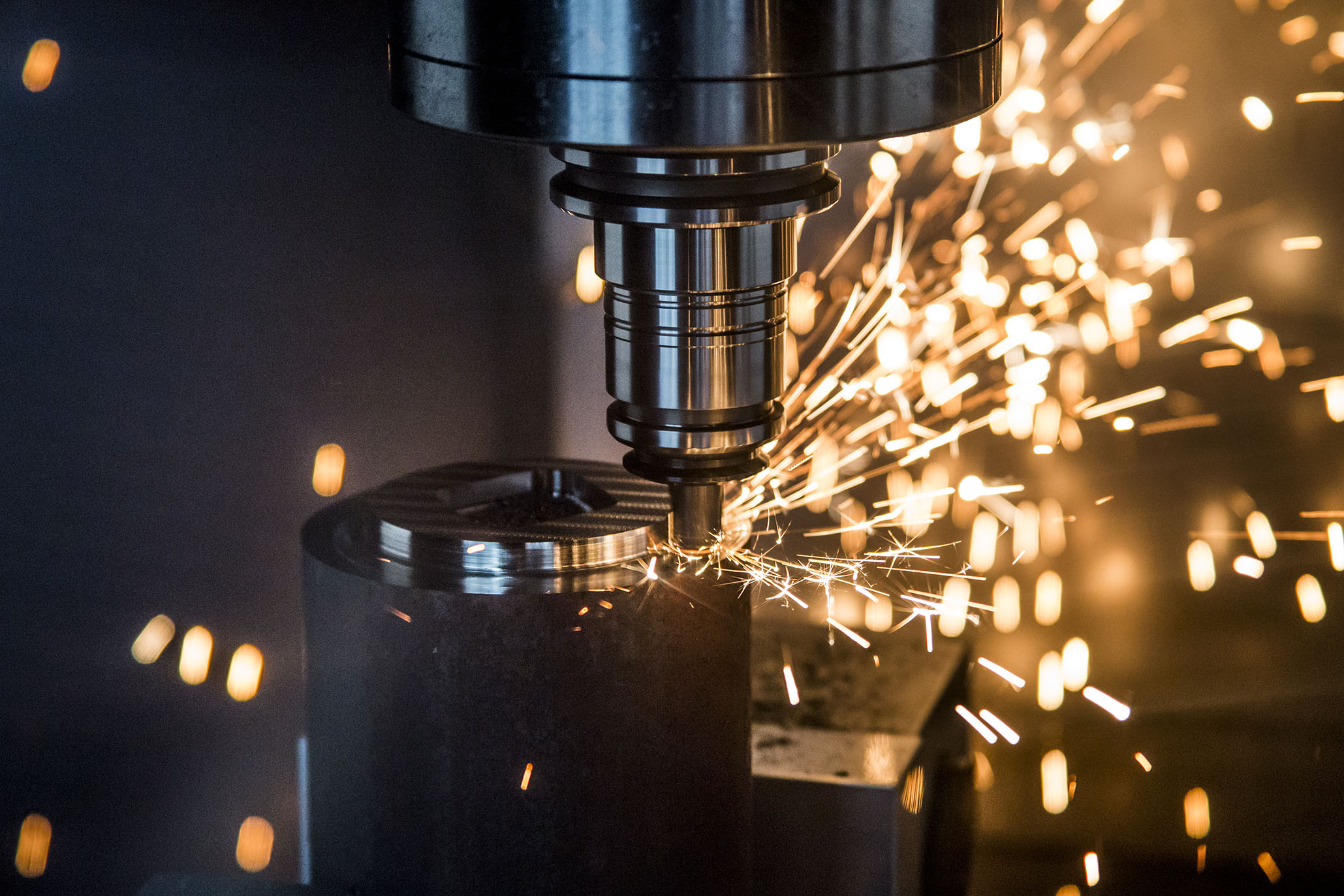
Whenever a discussion turns to standard tools (catalog) vs. specials (custom-designed tools), some interesting distinctions arise. For end users, the distinctions are straightforward. OEMs, job shops, and manufacturers up and down the supply chain—whether in automotive, aerospace or general engineering—want to know what, how soon and how much.
Cutter Considerations for Turning Titanium
Published February 10, 2022
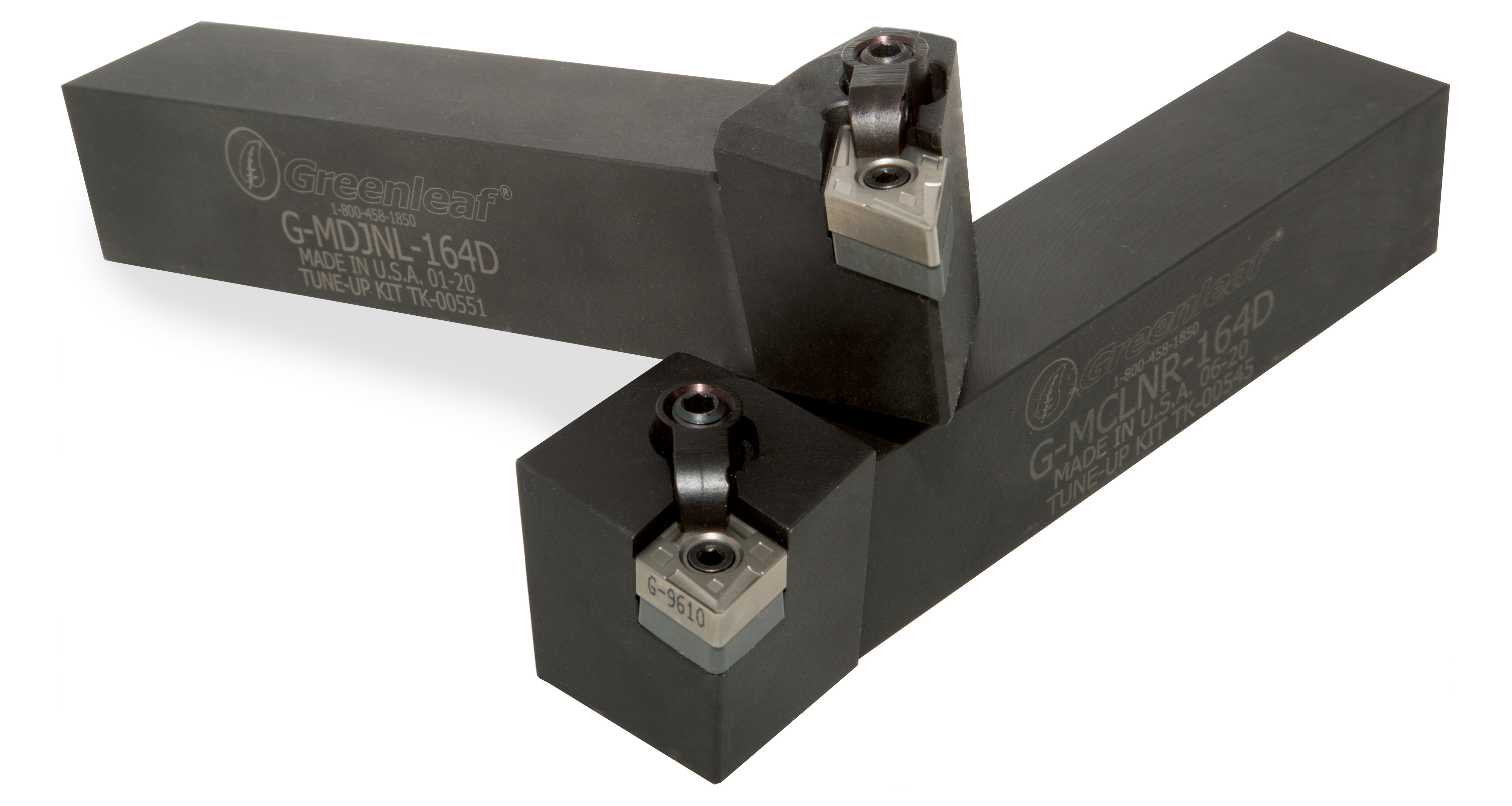
Greenleaf’s G-9610 is a PVD-coated carbide grade designed for turning titanium-based alloys. The wear-resistant, chemically stable and lubricious coating is said to protect the heat-resistant, submicron substrate and enable higher speeds and extended tool life in continuous cuts.
Aerospace Forecast
Published February 4, 2022
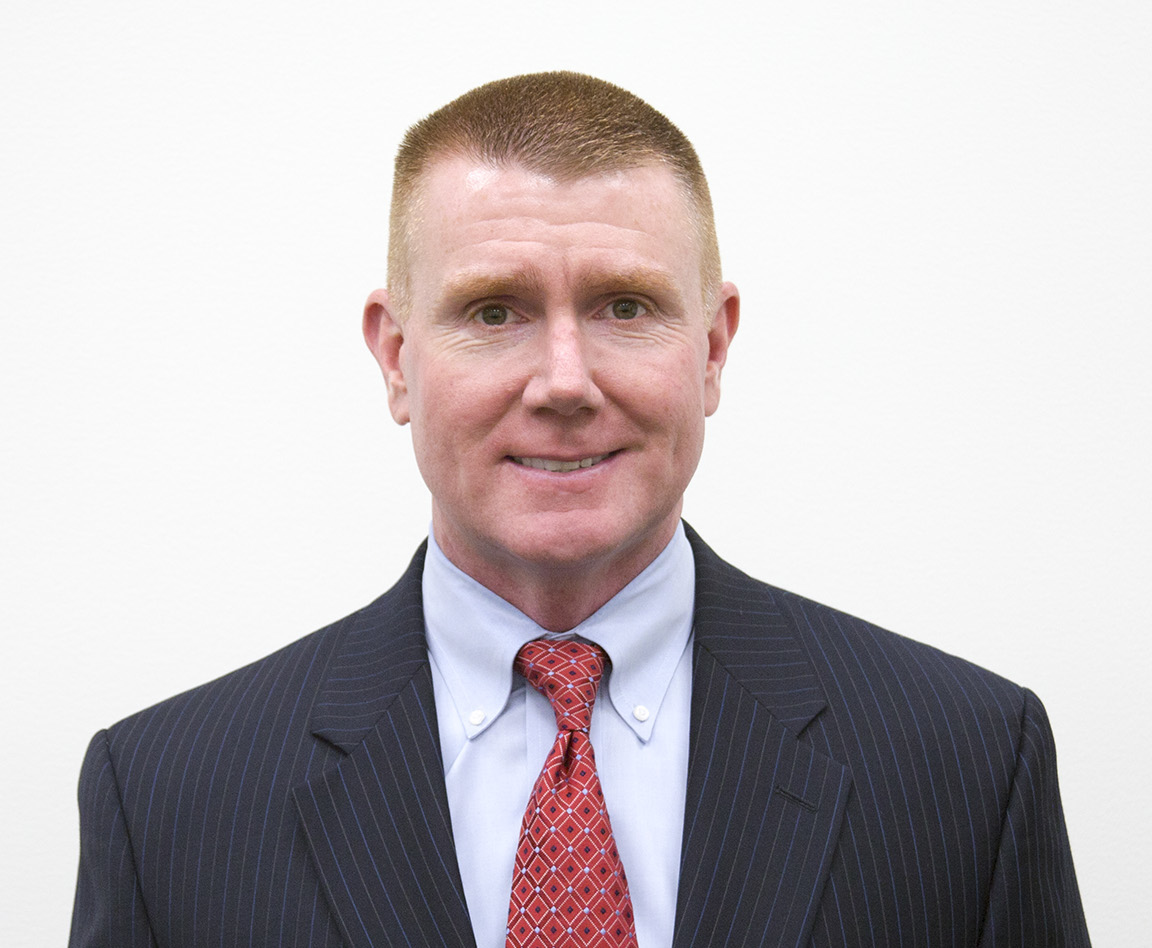
Maintaining a happy, healthy, and productive workforce is always top of mind for business leaders; but in today’s environment with more than 11 million job openings, and unemployment at record lows, this must be your primary focus.
Rake Angles Make or Break Facemilling
Published January 18, 2022
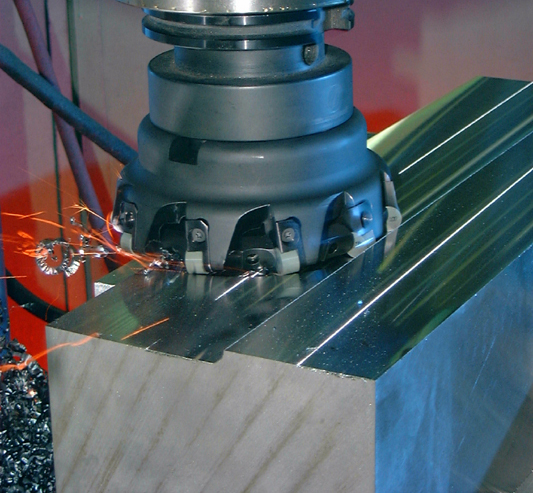
There are two types of rake angles. The axial rake angle is the angle between the cutting edge and the axis of the cutter. This angle affects the facemilling process in several ways. It directs chip flow and impacts cutting-edge strength. In addition, toolmakers use the axial rake angle to control power consumption, said Nate Peters, senior tool design engineer at Greenleaf Corp. in Saegertown, Pennsylvania.