Phase-Toughened Ceramics: The Next Revolution in Machining of Heat-Resistant Super Alloys
Alex Minich, Greenleaf Corporation
Published March 2019As a means of large-scale production, metal machining mostly developed throughout the 19th century, playing a significant role in the second industrial revolution and facilitating the manufacturing boom that fueled the technological expansion of the 20th century. While softer metals like copper and aluminum could be machined with relative ease, steel was more of a challenge. The invention of high-speed steel and cemented carbide in the early 20th century addressed these needs, but material requirements continued to grow. Increasing temperatures and stresses in gas turbines (among others) led to the development of nickel- and cobalt-based heat-resistant super alloys (HRSA), and while cemented tungsten carbide tools continued to improve – the rapidly evolving properties of HRSAs meant that carbide machining was, respectively, becoming less and less efficient.
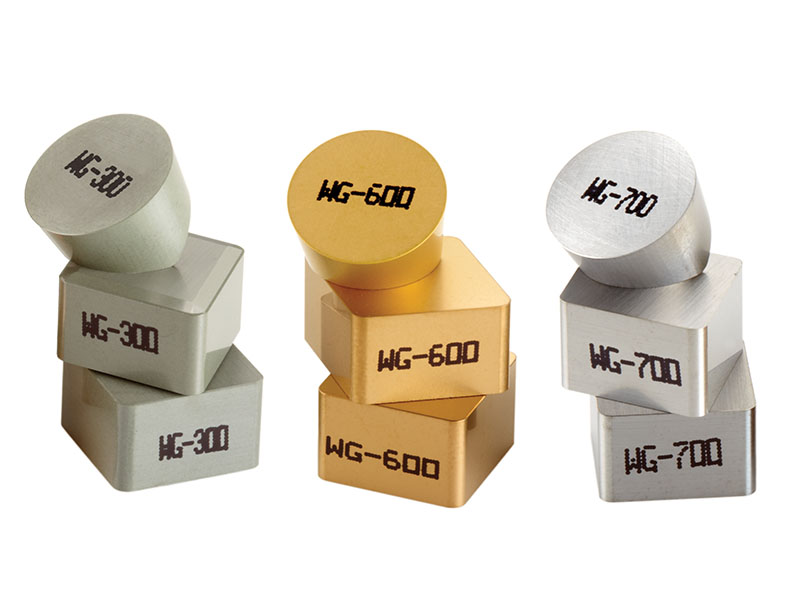
It wasn’t until the mid-1980s that a cutting tool material became commercially available that enabled reliable, repeatable high-speed machining of HRSAs. We are, of course, referring to WG-300® – a whisker-reinforced ceramic. It could be said that WG-300® did for the machining of nickel-based precipitation-hardened alloys what HSS and cemented tungsten carbide did for machining of steel. For the most part, machining with whisker-reinforced ceramics follows the same general principles that machining with carbide does – the cutting tool material is significantly harder than the materials it is used to machine, and it is applied to deform the surface layer of the machined component at very high strain rates, causing the machined material to fail in shear and separate – forming a chip. Beyond this general principle, both carbide and ceramics generate a significant amount of heat that is most concentrated on the cutting edge. A portion of this heat remains in the workpiece, propagating slightly ahead of the shear zone and reducing the strength of the bonds between adjacent atoms by raising their kinetic energy – a mechanism known as plasticization. What makes machining with ceramics so different is that the heat that is generated and the subsequent degree of plasticization are much higher.
Whisker-reinforced ceramics as they are known today are commonly SiC crystals embedded in an Al2O3 matrix. Randomly oriented SiC crystals reinforce the very inert and very hard (and rather brittle) Al2O3s matrix, lending toughness, reliability, and resistance to crack growth. The product is an isotropic material that retains hardness well beyond 1400°C, is tough enough to withstand the dynamic mechanical stresses of the machining process, and reliable enough to wear predictably and consistently when applied at the correct cutting parameters. The switch from carbide to whisker-reinforced ceramics, however, is not as straightforward as simply replacing an insert and turning the speed up. No, machining with ceramics places an emphasis on heat management that is far more substantial than it ever was in carbide machining. In fact, the single most important consideration when machining HRSAs with whisker-reinforced ceramics is to maintain a constant distribution of heat throughout the cut – evacuating the right amount of heat with the chip (ideally, circa 80%) and directing 10% of all heat generated into the workpiece, plasticizing it, reducing the cutting forces. The temperatures required to reach this degree of plasticization in common HRSAs (Inconel 718, Waspaloy, Hasteloy, etc.) are too high for the cobalt binder of cemented tungsten carbide tools, which is why the speeds reachable with whisker-reinforced ceramics are not feasible for carbide.
Switching from carbide to ceramics requires rethinking how the part is machined, to minimize mechanical stresses (resulting from, for example, high-feed straight entry into the cut) and keep the heat distribution constant. Higher cutting speed is the main reason why whisker-reinforced ceramics are more efficient than carbide in the machining of HRSAs, but it is also a necessity. Not having enough speed results in insufficient plasticization, which leaves the material ahead of the cut too cold and the bonds between the atoms too strong, lowering tool life. One of the most common modes of wear that can be seen when applying whisker-reinforced ceramics in nickel-based HRSAs is notching. Notching occurs as a result of chemical wear and mechanical abrasion – the work-hardened layer on the surface generates more heat than the material deeper in the cut, which, combined with the availability of oxygen, leads to the rapid decomposition and ablation of the (softened by the high heat) cutting tool at the workpiece-atmosphere boundary.
To minimize notching and ensure that the edge stays intact for as long as possible, it is generally recommended to use round inserts at a radial engagement of circa 45° or, whenever possible, continuously vary the depth of cut thereby spreading the depth-of-cut wear over the length of the cutting edge engaged. But varying the depth of cut with a round insert also means varying the lead angle and so, varying the chip thickness. The maximum chip thickness for a crescent-shaped chip (as opposed to the total cross-sectional area of the chip) is an appropriate variable for gauging heat evacuation. If the chip thickness is too low for the chosen speed, the chip becomes saturated with heat (which can also be noted from the discoloration of the chips – shading towards blue in nickel-based HRSAs) and the optimal 80-10-10 heat distribution is disturbed, resulting in higher temperatures in the cutting zone and faster wear of the cutting tool. If the chip thickness is too high, the chip carries away too much of the heat, resulting in insufficient plasticization and higher mechanical stresses (also because the chip is heavier).
Let us consider two common applications of whisker-reinforced ceramics in the machining of nickel-based HRSAs – (A) doing a straight cut on a 45 HRc Inconel 718 part to remove forging scale, and (B) profiling a pocket in clean 45 HRc Inconel 718 (say, on the internal diameter of a disk).
(A) Regardless of how close the forged part is to net shape or how light the scale is – there will always be an unevenness to the cut and a steep hardness gradient – because the part deforms from internal stresses introduced in the subsequent heat treatment, because of the forging process itself, or due to other external factors. The difference in hardness (and abrasiveness, if the material is prone to precipitation hardening) between the forging scale and the clean material deeper in the workpiece is considerably higher than the analogous difference between a work-hardened layer left after a prior machining process and the clean material deeper in the workpiece. This difference in hardness means that the heat generated at the workpiece-atmosphere boundary (where one would expect to see notching) is much higher than it is on the outermost part of the cutting edge (in clean material deeper in the component). This, in turn, leads to a significant disparity in plasticization regimes, mechanical stresses, and primary modes of wear along the portion of the cutting edge engaged. The added possible distortion to the flatness and roundness of the workpiece mean that the cut can be uneven – with variability of depth of cut and engagement along every revolution – requiring toughness and high edge strength. The best style of whisker-reinforced ceramic insert for this application is typically an RNGN-120700 or larger – the strongest insert shape possible. The challenge then, is to find a set of cutting data such that the heat generated at the surface is not too high, and the heat generated deeper in the material is not too low; the chip thickness is, on average, appropriate for the heat generated but does not create mechanical and thermal shock that could lead to irregular wear and reduced tool life. With an RNGN-120700-T1A in WG-300® this would be circa Vc = 275m/min, Fn = 0.18mm/rev, Ap = 3mm.
(B) Discarding for the time being the possibility of grooving (which is by far the fastest means of removing material to create a cavity), the most optimal style of insert that combines excellent edge strength, flank clearance required to feed into the material, fixation of insert in tool so as to counter cutting forces in a multitude of directions, and highest amount of useable cutting edges is an RCGX-120700 or smaller. To minimize notching, a whisker-reinforced ceramic V-bottom insert would be used to ramp into the material from 0 to max Ap, and then execute a straight cut with the opposite edge, also effectively ramping from 0 to max Ap. The challenge in this application is to vary the feed in such a fashion as to maintain a constant maximum chip thickness (which does not vary linearly with depth of cut) to maintain a constant balance of heat. This also means reducing the feed when approaching the shoulder, because the depth of cut then (at a shoulder perpendicular to the direction of feed) grows to the radius of the insert. For an RCGX-090700-T1 in WG-300® the cutting data would be Vc = 350m/min, Fn = 0.25-0.08mm/rev, Ap = 0-1.6mm.
Enter phase-toughened ceramics – in 2016 Greenleaf introduced XSYTIN®-1. Its microstructure and chemistry differ from a common SiAlON or whisker-reinforced ceramic. XSYTIN®-1 is created in a uniquely controlled environment that results in the synthesis of interlocked grains, forming a reinforced structure that resists the nucleation of cracks in an unprecedentedly wide array of applications. This toughening mechanism, combined with the high strength of the individual grains results in a cutting tool that has material properties unlike any other. The transverse rupture strength of XSYTIN®-1 (the amount of stress a sample of material is able to sustain in bending) is approximately twice that of WG-300®, allowing a significant increase in static loading that translates directly to higher optimal chip thickness. It is extremely resistant to thermal shock, and will maintain a sharp cutting edge in a wide range of plasticization regimes. All-told, XSYTIN®-1 has the capacity to once again revolutionize the machining of HRSA where other ceramics would only offer slight incremental improvements.
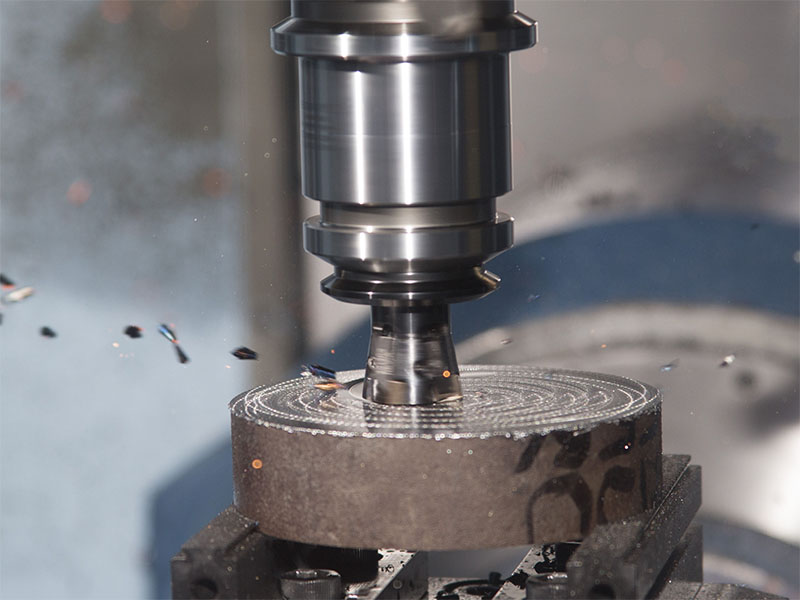
Let us reconsider (A) and (B) with XSYTIN®-1 in mind.
(A) The ability to apply XSYTIN®-1 effectively in a wide range of plasticization regimes means that finding a cutting speed to eliminate notching at the workpiece-atmosphere boundary will not result in uneven wear in clean material below the scale. The same principle applies to clean turning but is especially beneficial in the removal of scale. The extreme edge strength and toughness of XSYTIN®-1 imply that one is no longer required to use a round insert – a straight-edged insert at a 45° lead angle will generate lower cutting forces at higher depths of cut than an RNGN, maintaining predictable wear even in interrupted cuts. One such example was the use of an SNGA-190616E (in a toolholder designed for carbide with only a pin to secure the insert) to remove forging scale in Inconel 718 at 45 HRc (see Fig. 1). The optimal cutting conditions were Vc = 200m/min, Fn = 0.3mm/rev, Ap = 5mm – doubling the rate of metal removal of WG-300®.
(B) The ability to eliminate notching by machining in a lower plasticization regime eliminates the need to ramp. It was also recently found that at optimal chip thickness (~0.18mm in 45 HRc Inconel 718) and with the application of high-pressure coolant, increasing the depth of cut with a round insert (E edge preparation, XSYTIN®-1) past 50° radial engagement (~Ap = 2.2mm for a 12.7mm insert) changes the flow of the chip: the curvature is too high for the chip to stay intact and it fragments before rebounding from the surface of the insert – eliminating crater wear entirely and extending tool life (see Fig. 2). With all that in mind, the best strategy to open a pocket with RCGX-090700E in XSYTIN®-1 is trochoidal turning (see Fig. 3) at Vc = 250m/min, Fn = 0.3mm/rev, Ap = 1.7mm – 2.75x faster than ramping with whisker-reinforced ceramics.
In many cases (e.g. whenever the machine does not have enough power or rigidity to make full use of XSYTIN®-1) whisker-reinforced ceramics are still the best cutting tool for the job. But even without the tremendous increase in productivity, there are applications where the exceptional properties of XSYTIN®-1 make it the only cost-effective ceramic cutting tool. N18, Udimet 720, Rene-88, Haynes-282, ML340 and various other last-generation high-strength alloys are some materials in which the toughness and edge strength of XSYTIN®-1 allow significantly reducing cycle time and/or extending tool life compared to other cutting tools.
< Back to 2019 Archives